Necessary Tools and Devices for Effective Metal Stamping Operations
Necessary Tools and Devices for Effective Metal Stamping Operations
Blog Article
Unlocking the Power of Metal Stamping: Strategies for Improved Item Advancement
In the realm of manufacturing, the usage of steel stamping holds a significant area as a result of its convenience and performance in generating elaborate parts and parts. Nevertheless, real possibility of steel marking remains untapped by many companies seeking to enhance their item development procedures. By checking out sophisticated strategies and methods customized to maximize design, material selection, production performance, and quality control, companies can open a wealth of opportunities to boost their products to new heights of development and efficiency.
Advantages of Steel Stamping
Metal stamping offers a efficient and cost-effective technique for generating top notch steel parts. One of the vital advantages of steel stamping is its capacity to produce complex geometries with high precision and uniformity.
Moreover, steel stamping enables high-volume manufacturing, making it ideal for tasks that require large amounts of steel components. The speed and repeatability of the stamping process not just ensure expense financial savings yet also add to faster turn-around times for production orders. In addition, making use of automated equipment in metal marking assists decrease the risk of human error, causing improved general product quality.
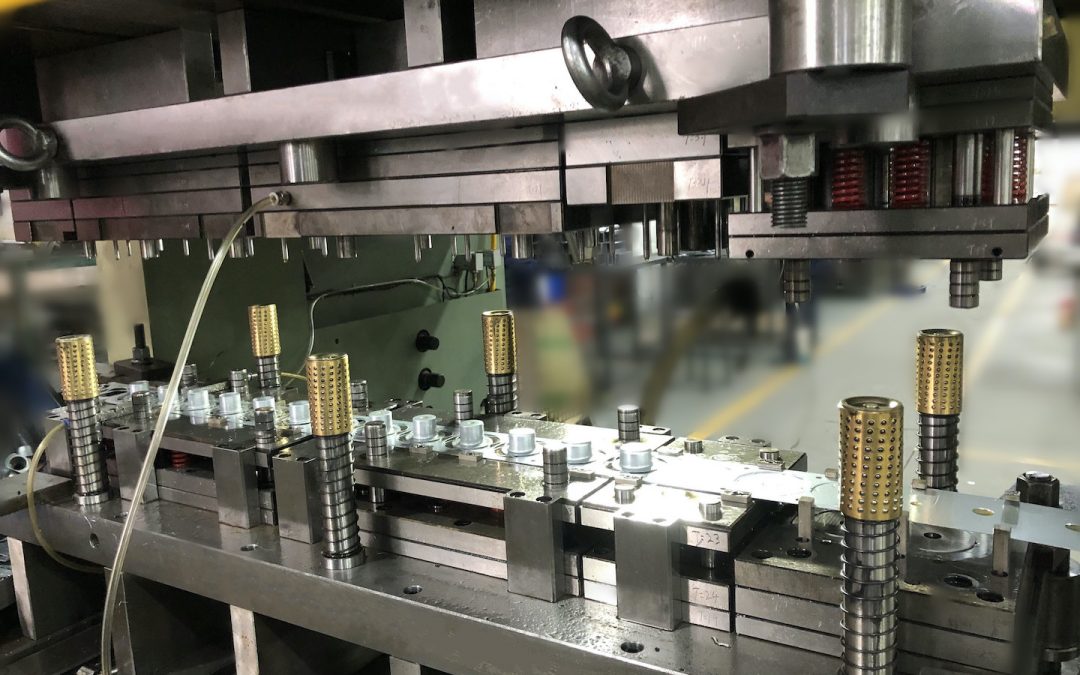
Style Optimization Techniques
With careful factor to consider of material homes and geometric configurations, layout optimization methods play an important function in improving the efficiency and performance of metal stamping procedures. By purposefully evaluating factors such as material thickness, stamina, and kind, suppliers can tailor the layout to maximize the efficiency of the marking procedure. Utilizing simulation software, designers can anticipate just how various layout variants will act under numerous marking conditions, enabling for the recognition of prospective concerns before manufacturing begins.
Additionally, incorporating attributes like fillets, chamfers, and embosses right into the design can enhance the general quality of the stamped part while minimizing the risk of defects such as splitting or contorting. Additionally, optimizing the layout of attributes on the component can enhance the product circulation throughout marking, causing even more constant and specific results.
Fundamentally, design optimization techniques allow producers to adjust their steel stamping processes, bring about improved item top quality, raised manufacturing performance, and ultimately, a more competitive setting in the market.
Material Choice Approaches
Design optimization methods in steel stamping processes heavily depend on tactical material option strategies to make certain the desired efficiency and efficiency of the produced parts. The selection of product in metal stamping is important as it directly affects the quality, toughness, and overall capability of the end product. When choosing the suitable product for a particular task, factors such as mechanical properties, formability, cost-effectiveness, and deterioration resistance should be taken into account.
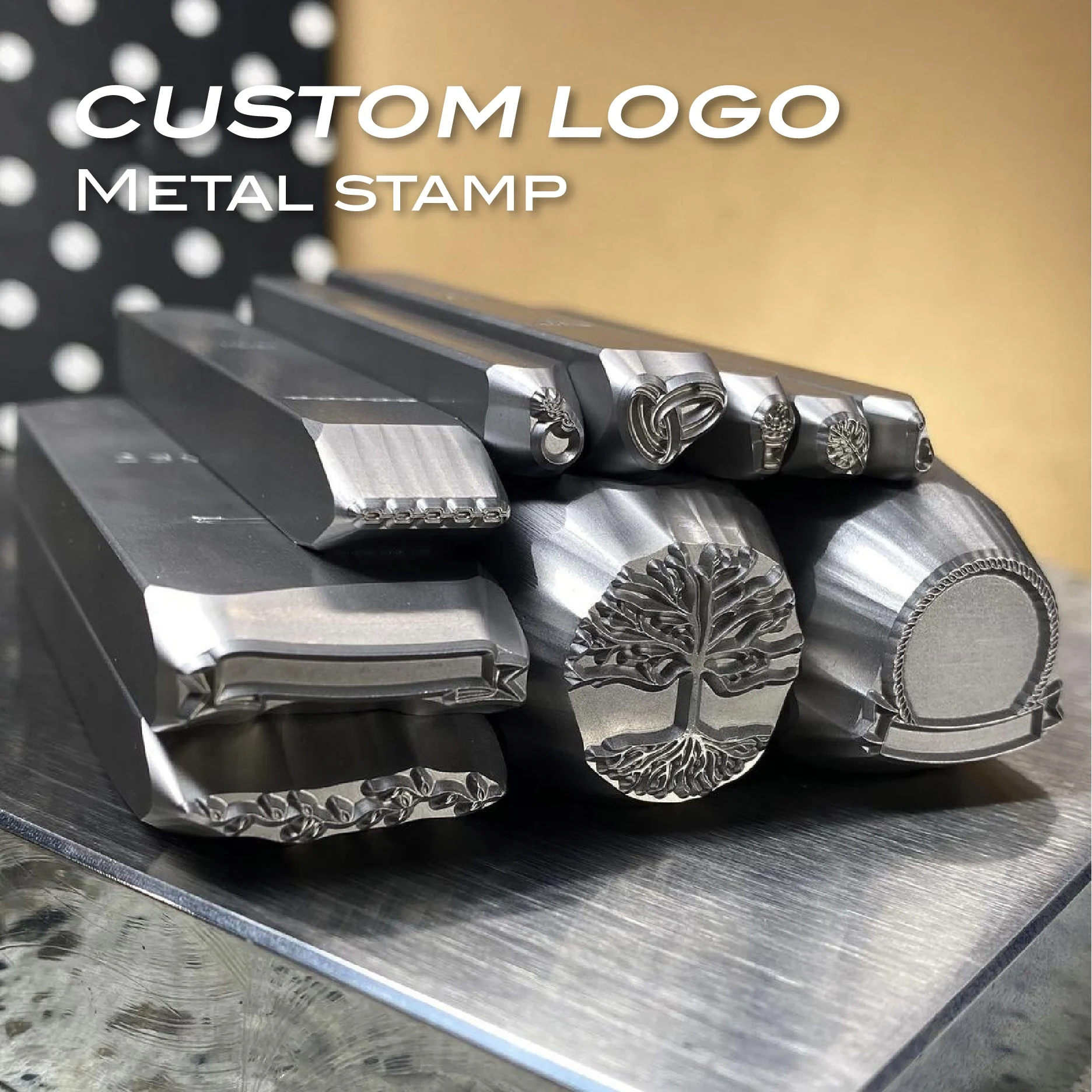
Stabilizing the performance requirements with the general price of products is essential to make sure the financial stability of the production process. By very carefully assessing these facets, makers can enhance their material option strategies to achieve premium product quality and operational efficiency.
Enhancing Production Efficiency
Efficiency in manufacturing processes is an essential variable for ensuring cost-effectiveness and timely distribution of top notch metal stamped components. To enhance manufacturing see this effectiveness in steel stamping, numerous approaches can be applied. One crucial strategy is enhancing the tooling style to reduce material waste and decrease production time. By using sophisticated simulation software application, producers can fine-tune the tooling and evaluate style prior to actual production, thereby streamlining the stamping process and boosting overall efficiency.
In addition, implementing automation and robotics in steel stamping operations can dramatically raise productivity and uniformity while decreasing labor expenses. Automated systems can execute repeated tasks with high precision and speed, bring about improved manufacturing efficiency and higher outcome prices. Investing in contemporary marking tools with innovative functions, such Learn More as servo-driven presses and fast die change systems, can additionally optimize manufacturing processes and minimize downtime.
Moreover, developing clear interaction channels and promoting collaboration between production, layout, and engineering teams is critical for identifying potential traffic jams and applying continuous renovations in the production process - Metal Stamping. By embracing lean production principles and leveraging technology developments, producers can open the full possibility of steel stamping procedures and accomplish better manufacturing effectiveness
High Quality Control and Examination Approaches
To guarantee the consistent manufacturing of premium metal stamped parts, rigorous quality control and evaluation approaches play a pivotal function in verifying the precision and integrity of the manufacturing procedure. Quality control in steel stamping includes a series of organized checks and actions to assure that each component fulfills the specified demands. Evaluation approaches such as aesthetic exam, dimensional evaluation, and material screening are typically employed to assess the high quality of stamped parts. Visual assessments make sure the surface coating and integrity of the parts, while dimensional evaluation validates that the parts satisfy the required requirements. Product testing methods like solidity screening and material make-up evaluation assistance verify the material properties and structural stability of the stamped parts. In addition, progressed technologies such as automated optical examination systems and coordinate gauging devices are significantly being utilized to improve the accuracy and performance of quality assurance processes in metal marking. By executing durable quality assurance and evaluation methods, manufacturers can maintain high requirements of high quality and uniformity in their steel stamped products.
Conclusion
In final thought, metal stamping offers many advantages such as cost-effectiveness, precision, and convenience in item advancement. Overall, opening the power of steel stamping calls for a tactical method to enhance item development processes.
Steel marking deals a cost-efficient and effective method for creating top notch metal elements.Additionally, metal marking permits for high-volume manufacturing, making it suitable for tasks that call for large quantities her latest blog of metal parts.Through cautious factor to consider of product homes and geometric configurations, layout optimization techniques play an important function in boosting the effectiveness and capability of steel stamping procedures.Layout optimization methods in metal marking processes greatly rely on calculated material option approaches to guarantee the wanted performance and efficiency of the made components. The option of material in metal marking is essential as it straight influences the top quality, longevity, and overall performance of the last product.
Report this page